What Is Residual Stress Analysis?
Non-destructive residual stress analysis for metals
Residual stress may be created during the manufacturing process of a material, or it may accumulate in a structure over many years in operation. In either case, this stress can have a serious negative effect on a product's quality, durability and lifetime. Accurate detection of residual stress is an important element of the quality control process and helps predict the service lifetime of products.
X-ray diffraction (XRD) is presently the only accurate way to non-destructively measure residual stress. In addition, XRD offers non-contact measurements with unsurpassed spatial resolution and the ability to measure hardened materials. Residual stress, of either exceptionally strained points or the surfaces of moving parts, is routinely determined by XRD. To meet the requirements of these tasks, Rigaku offers several systems to allow flexible component and sample handling for every budget and need.
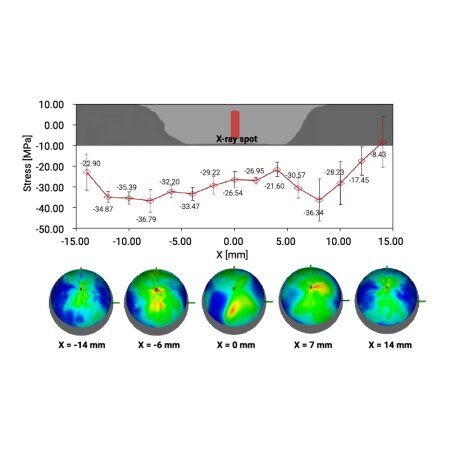
Rigaku recommends the following products
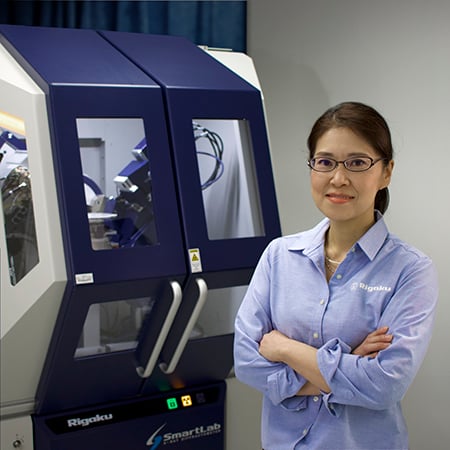
Contact Us
Whether you're interested in getting a quote, want a demo, need technical support, or simply have a question, we're here to help.